CNC and precision machining in Copper
Specification of CNC machining parts with Copper
CNC machining copper refers to the process of machining copper parts using Computer Numerical Control (CNC) machines. This process involves the use of cutting tools, such as drills and end mills, to shape copper into the desired shape and size. The CNC machining process is highly precise, allowing for complex shapes to be created with a high degree of accuracy.
The most common type of copper used for CNC machining is C110. This type of copper is ideal for CNC machining due to its high malleability and strength. Other copper alloys, such as C145 and C175, may be used for CNC machining depending on the application.
The cutting tools used for CNC machining copper must be made of high-speed steel or carbide. These materials are able to withstand the high temperatures generated during the machining process. Additionally, the cutting tools must be sharp and properly lubricated to ensure efficient machining.
The CNC machining process also requires the use of coolant to help remove chips and particles from the workpiece. Additionally, the coolant helps to reduce heat build-up and prolong the life of the cutting tool.
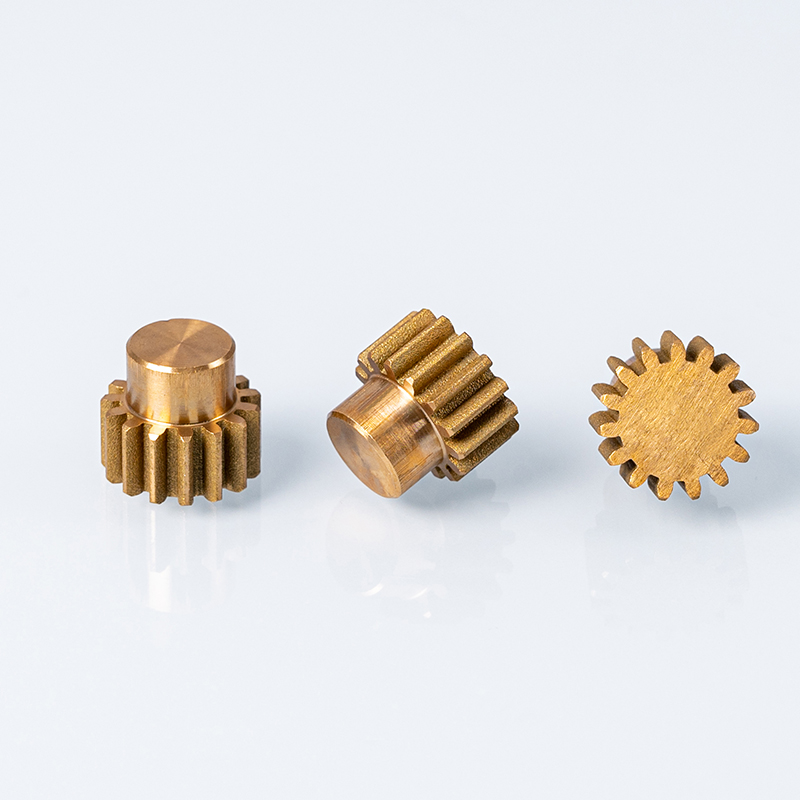
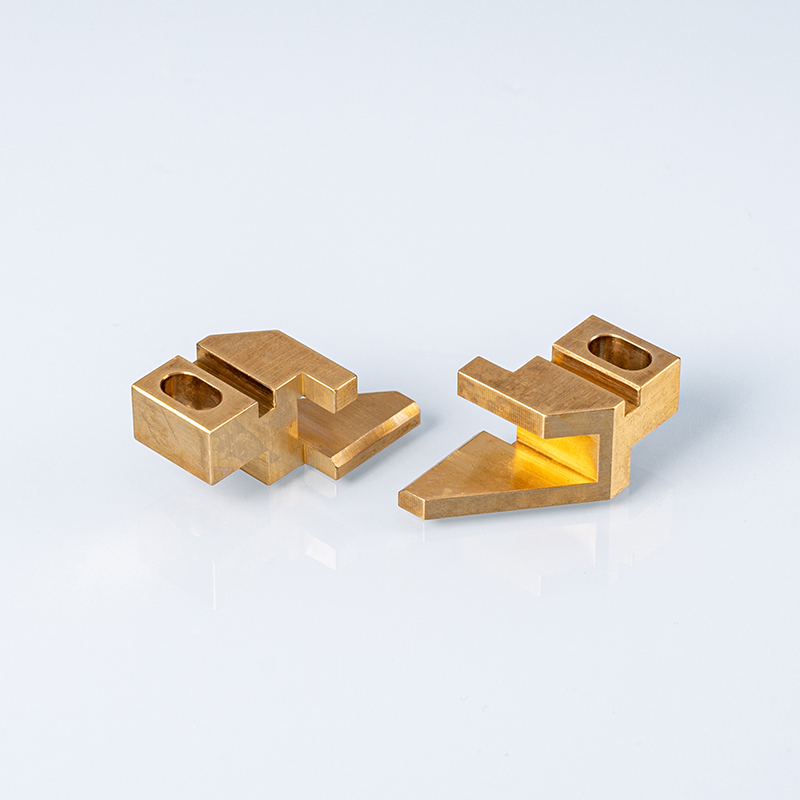
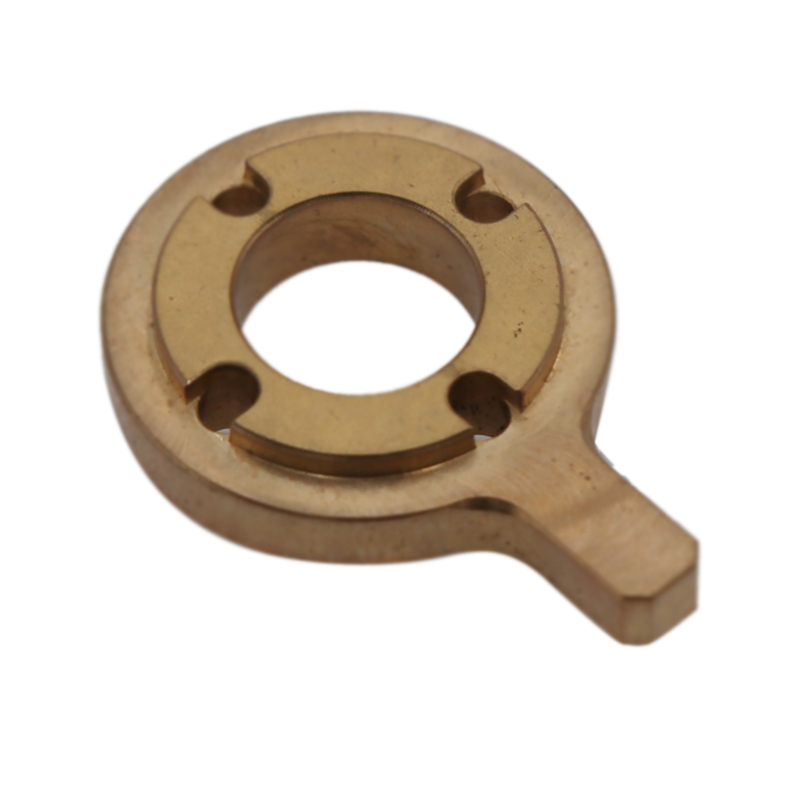
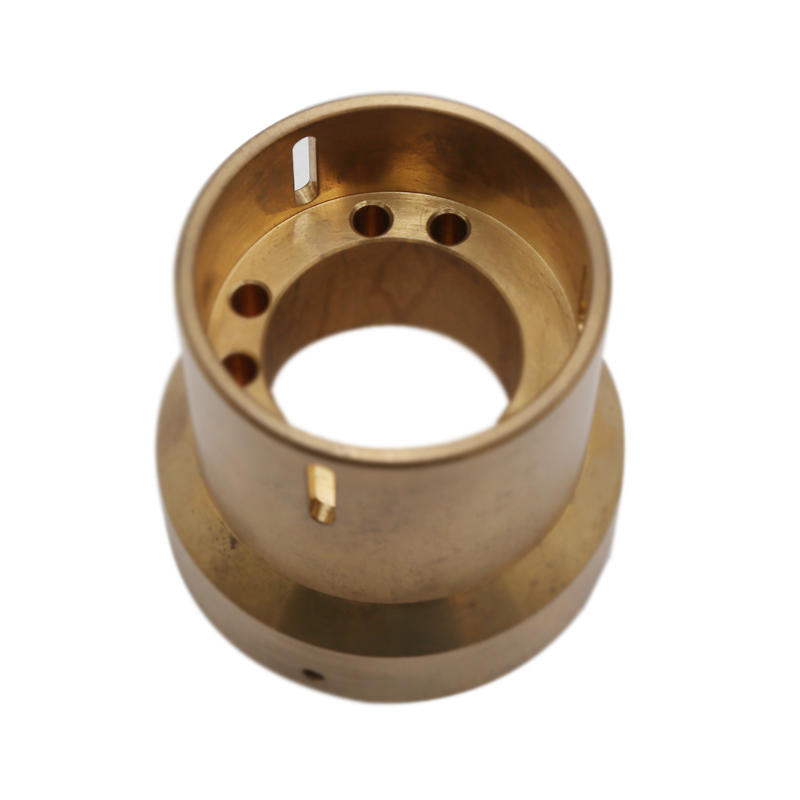
Advantage of CNC machining Copper
CNC machining copper offers many advantages, such as high precision and accuracy, excellent strength-to-weight ratio, good thermal and electrical conductivity, increased corrosion resistance compared to other metals, dimensional stability over a wide temperature range, reduced machine time due to its malleability and ease of machinability.
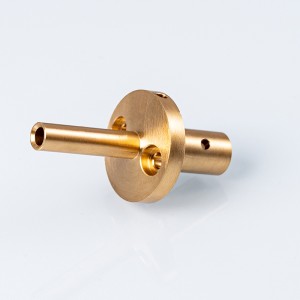
1. Superior strength and durability – Copper is an extremely durable material and is able to withstand high temperatures, pressure and wear. This makes it an excellent choice for CNC machining applications, as it can be used in a wide variety of applications and is able to withstand the rigors of repetitive, high-precision machining operations.
2. Excellent thermal conductivity – Copper's excellent thermal conductivity makes it ideal for CNC machining applications that require precision cutting and drilling operations. This ensures that the finished product will have the highest level of accuracy and precision.
3. High electrical conductivity – This feature makes copper an ideal material for CNC machining operations that require electrical wiring or components.
4. Cost-effective – Copper is generally less expensive than other metals, making it the perfect choice for CNC machining projects that require a large number of parts or components.
5. Easy to work with – Copper is an easy material to work with, allowing for faster production and greater accuracy.
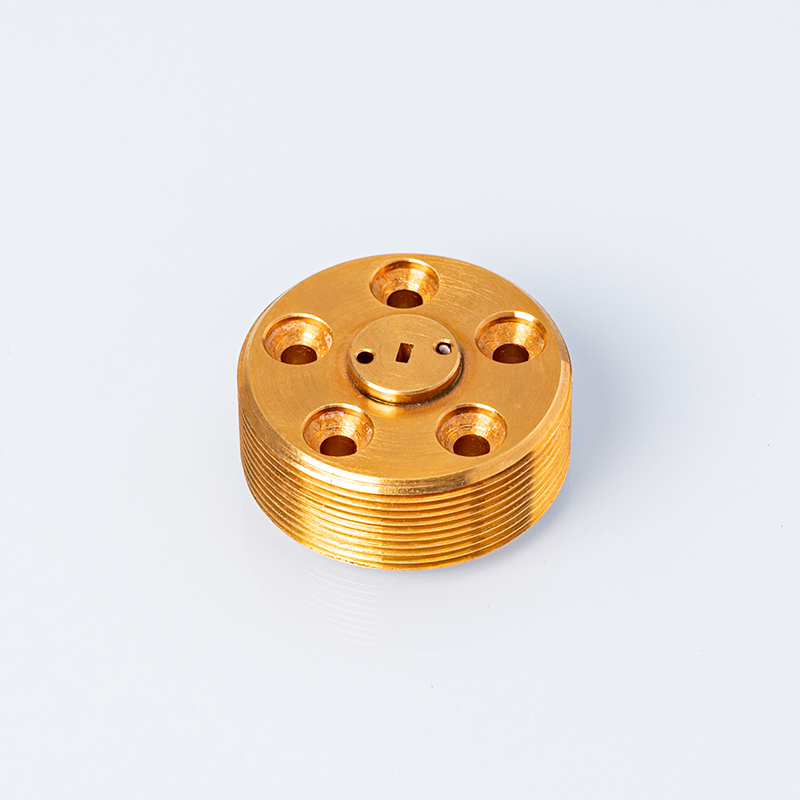
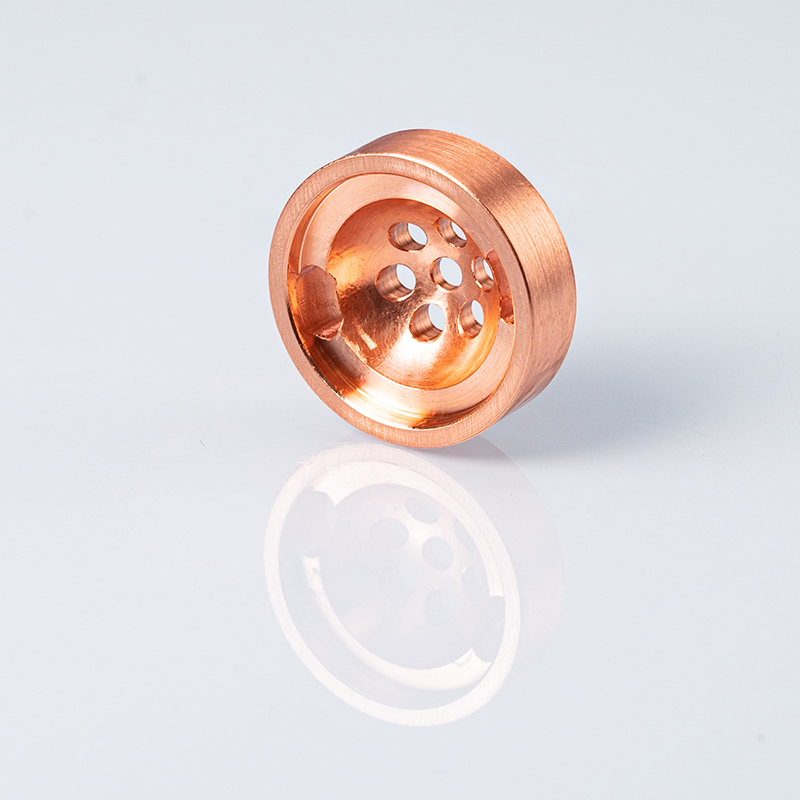
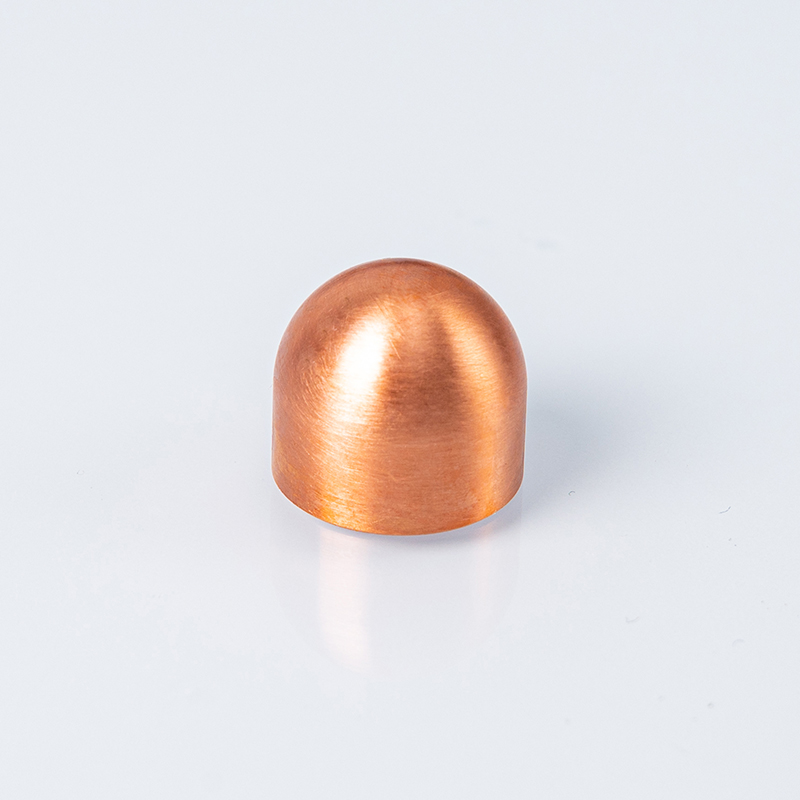
How Copper in CNC machining parts
CNC machining copper parts involves the use of precision cutting tools such as end mills to remove material from the workpiece according to a programmed path. The programming for CNC machining is done through computer-aided design (CAD) software and is then transferred to the machine via G code, which allows it to process each movement in turn. Copper parts can be drilled, milled or turned depending on the application. Metalworking fluids are also commonly used during CNC machining processes, particularly when dealing with harder metals like copper that require extra lubrication.
CNC machining copper parts is a machining process of using computer numerical controlled (CNC) machines to shape copper materials. Copper is used in a variety of CNC applications including prototyping, molds, fixtures, and end-use parts.
CNC machining copper requires the use of specialized software and CNC machines that are equipped with the proper tools to accurately cut and shape the material. The process begins by creating a 3D model of the desired part in a CAD program. The 3D model is then converted into a tool path, which is a set of instructions that program the CNC machine to produce the desired shape.
The CNC machine is then loaded with the appropriate tooling, such as end mills and drill bits, and the material is then loaded into the machine. The material is then machined according to the programmed tool path and the desired shape is produced. After the machining process is complete, the part is inspected to ensure it meets specifications. If necessary, the part is then finished with a variety of post-machining processes such as buffing and polishing.
What CNC machining parts can use for Copper
CNC machining copper parts can be used for a variety of applications, including electronics components and connectors, high-precision automotive parts, aerospace components, medical equipment, complex mechanical assemblies and more. Copper CNC machined parts are often plated with other metals to improve conductivity or wear resistance.
CNC machining copper parts can be used for a variety of applications, including electrical connectors, motor housings, heat exchangers, fluid power components, structural components, and decorative components. Copper parts are ideal for CNC machining due to its high electrical and thermal conductivity, and its excellent corrosion resistance. CNC machining copper can also be used to create intricate shapes and parts with precise tolerances.
What kind of surface treatment is suitable for CNC machining parts of Copper
The most suitable surface treatment for CNC machining copper parts is anodizing. Anodizing is a process that involves electro chemically treating the metal and forming an oxide layer on the surface of the material which increases the wear resistance and corrosion protection. It can also be used to provide decorative finishes such as bright colors, matte finish or glowing tones.
Copper alloys are generally treated with electroless nickel plating, anodizing, and passivation to protect the surface from corrosion and wear. These processes are also used to improve the aesthetics of the part.
Application:
3C industry, lighting decoration, electrical appliances, auto parts, furniture parts, electric tool, medical equipment, intelligent automation equipment,other metal casting parts.