Alloy Steel CNC machining parts
Available materials
Alloy steel 1.7131 | 16MnCr5: Alloy steel 1.7131 is also known as 16MnCr5 or 16MnCr5 (1.7131) is a low alloyed engineering steel grade that is commonly used for a variety of applications. It is commonly used in gears, crankshafts, gearboxes, and other mechanical parts that require high surface hardness and wear resistance.
Alloy steel 4140 | 1.2331 | EN19 | 42CrMo: AISI 4140 is low alloy steel with chromium and molybdenum content ensuring reasonable strength. Moreover it has good atmospheric corrosion resistance. It is widely used in many industries due to its excellent properties.
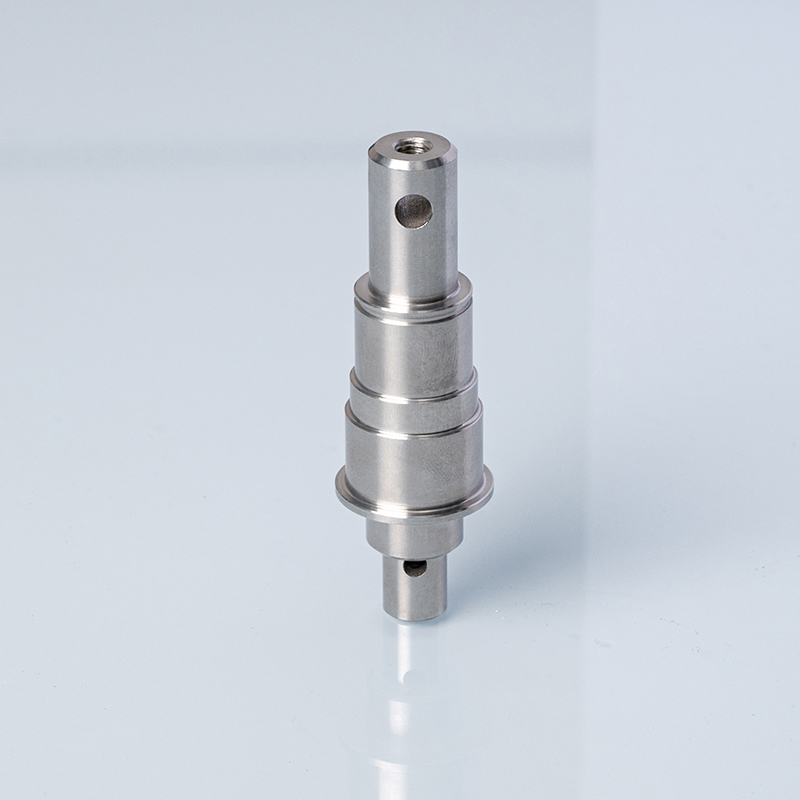
Alloy steel 1.7225 | 42CrMo4:
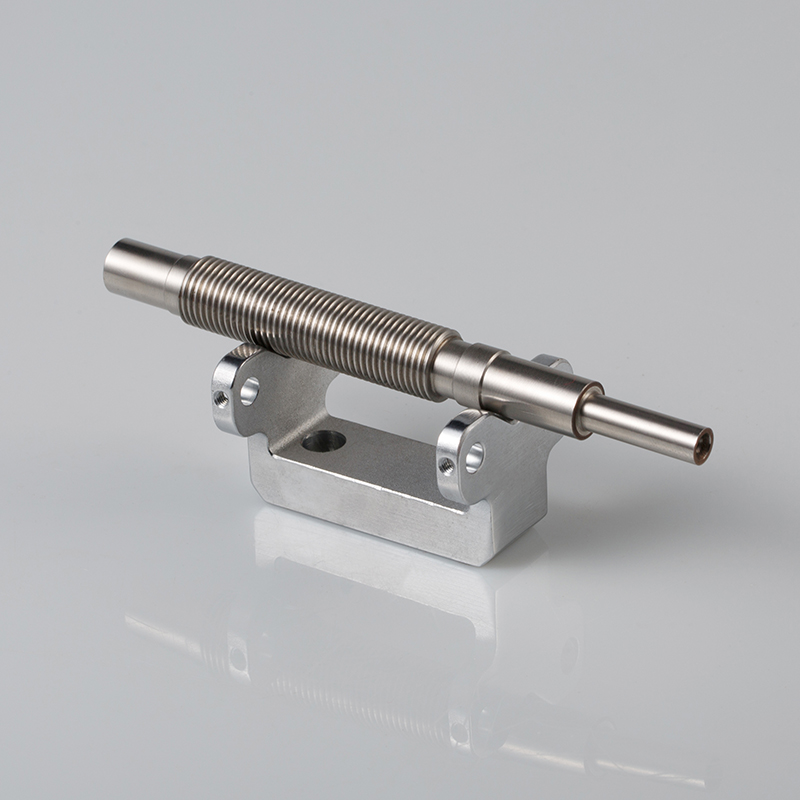
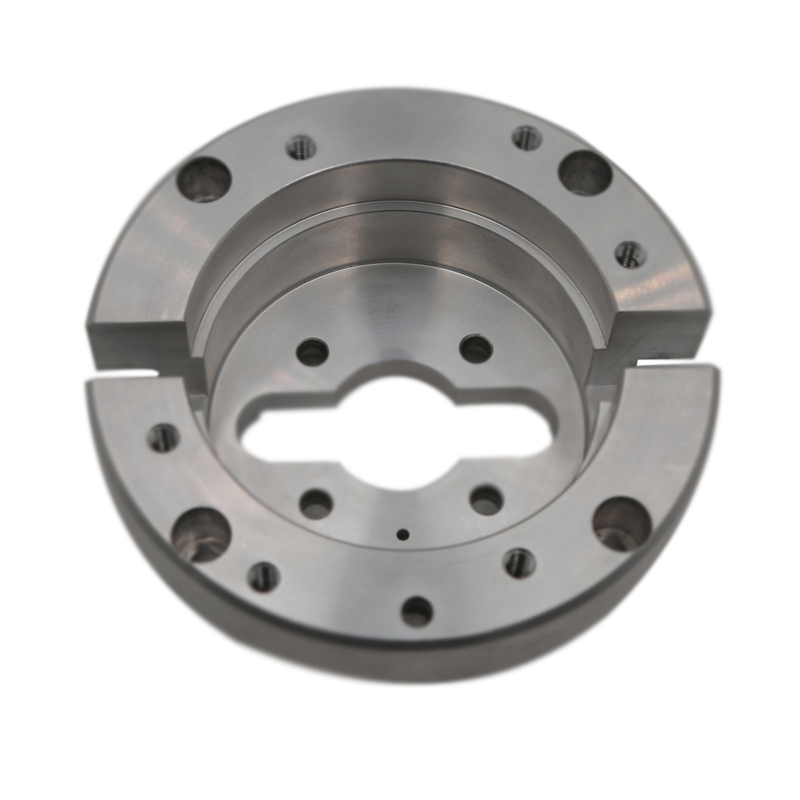
Advantage of Alloy steel
Alloy steel 4340 | 1.6511 | 36CrNiMo4 | EN24: Famous my its toughness and strength 4140 is medium carbon low alloy steel. It can be heat treated to high strength levels while maintaining good toughness, wear resistance and fatigue strength levels, combined with good atmospheric corrosion resistance, and strength.
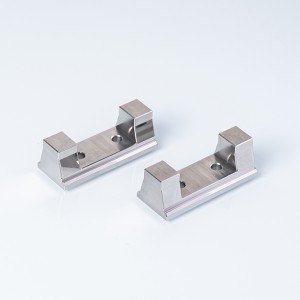
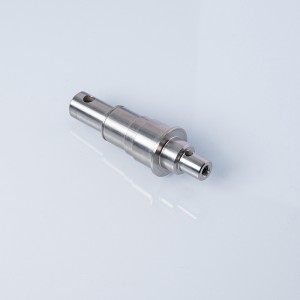
Alloy steel 1215 | EN1A :1215 is a carbon steel meaning that contains carbon as a main alloying element. It is often compared to carbon steel 1018 due to the similarity of their applications, but they have many differences. 1215 steel has better machinability and can hold tighter tolerances as well as a brighter finish.
What kind of surface treatment is suitable for CNC machining parts of Alloy steel material
The most common surface treatment for CNC machining parts of alloy steel material is black oxide. This is an environmentally friendly process which results in a black finish that is corrosion and wear resistant. Other treatments include vibro-deburring, shot peening, passivation, painting, powder coating, and electroplating.