What kind of special material will use in oil & Gas CNC machined parts?
CNC machined parts used in the oil and gas industry require special materials that can withstand high-pressure, high-temperature, and corrosive environments. Here are some of the special materials commonly used in oil and gas CNC machined parts along with their material codes:
When selecting a material for oil and gas CNC machined parts, it is important to consider the specific application requirements, such as pressure, temperature, and corrosion resistance. The material must be chosen carefully to ensure that the part can withstand the expected loads and environmental conditions and provide reliable performance over the intended service life.
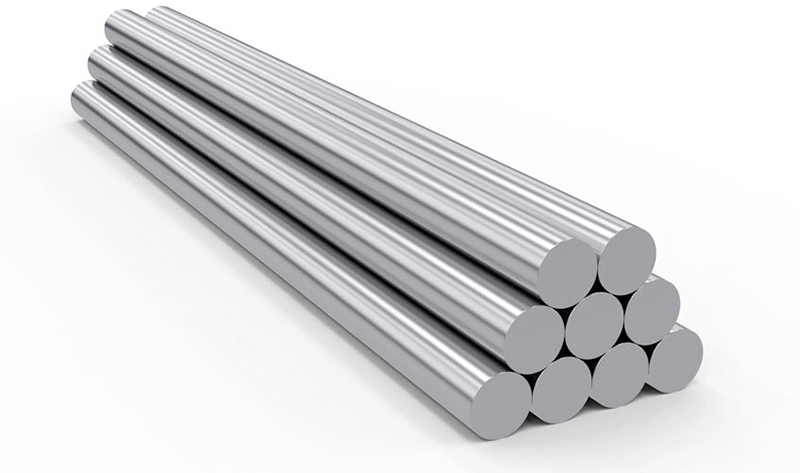
Oil Normal Material |
Oil Material code |
Nickel Alloy |
AGED 925,INCONEL 718(120,125,150,160 KSI),NITRONIC 50HS,MONEL K500 |
Stainless Steel |
9CR,13CR,SUPER 13CR,410SSTANN,15-5PH H1025,17-4PH(H900/H1025/H1075/H1150) |
Non-magnetic Stainless Steel |
15-15LC,P530,Datalloy 2 |
Alloy Steel |
S-7,8620,SAE 5210,4140,4145H MOD,4330V,4340 |
Copper Alloy |
AMPC 45,TOUGHMET,BRASS C36000,BRASS C26000,BeCu C17200,C17300 |
Titanium Alloy |
C.P. TITANIUM GR.4,Ti-6AI-4V, |
Cobalt-base Alloys |
STELLITE 6,MP35N |
What kind of special material will use in oil & Gas CNC machined parts?
Special threads used in oil and gas CNC machined parts must be designed to meet the specific demands of the application, such as high pressure, high temperature, and harsh environmental conditions. The most commonly used threads in the oil and gas industry include:
Regenerate response
When selecting a thread for oil and gas CNC machined parts, it is important to consider the specific application requirements and choose a thread that can withstand the expected loads and environmental conditions. It is also important to ensure that the thread is manufactured to the appropriate standards and specifications to ensure compatibility with other components in the system.
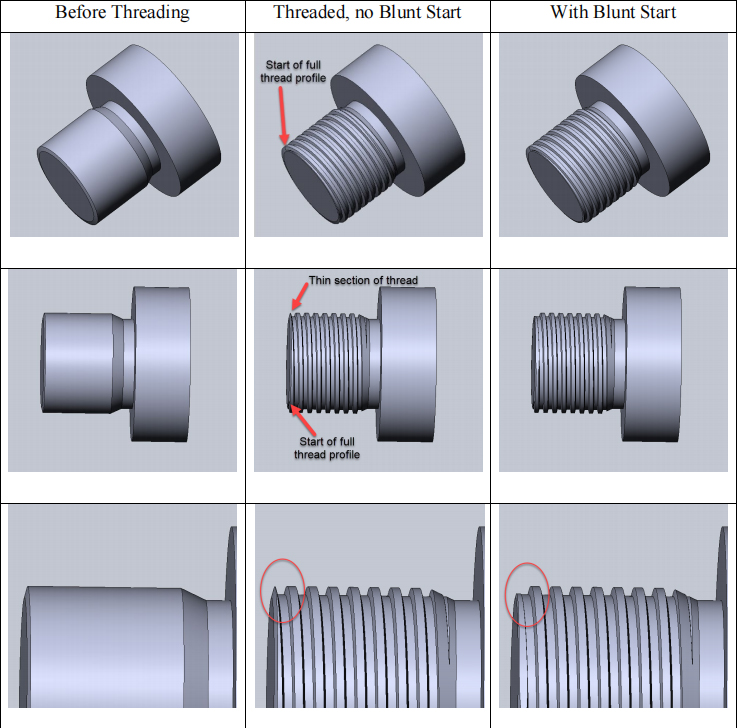
Here some special thread for reference:
Oil Thread Type |
Oil Special Surface Treatment |
UNRC Thread |
Vacuum electron beam welding |
UNRF Thread |
Flame sprayed (HOVF) nickel tungsten carbide |
TC Thread |
Copper Plating |
API Thread |
HVAF (High Velocity Air Fuel) |
Spiralock Thread |
HVOF (High Velocity Oxy-Fuel) |
Square Thread |
|
Buttress Thread |
|
Special Buttress Thread |
|
OTIS SLB Thread |
|
NPT Thread |
|
Rp(PS)Thread |
|
RC(PT)Thread |
What kind of special surface treatment will use in oil & Gas CNC machined parts?
Surface treatment of CNC machined parts is an important aspect of ensuring their functionality, durability, and longevity in the harsh conditions of the oil and gas industry. There are several types of surface treatments that are commonly used in this industry, including:
It is important to select the appropriate surface treatment based on the specific application and operating conditions of the CNC machined parts in the oil and gas industry. This will ensure that the parts are able to withstand the harsh conditions and perform their intended function effectively and efficiently.
HVAF (High-Velocity Air Fuel) &HVOF (High-Velocity Oxygen Fuel)
HVAF (High-Velocity Air Fuel) and HVOF (High-Velocity Oxygen Fuel) are two advanced surface coating technologies that are commonly used in the oil and gas industry. These techniques involve heating a powdered material and accelerating it to high velocities before depositing it onto the surface of the machined part. The high velocity of the powder particles leads to a dense and tightly adherent coating that offers superior resistance to wear, erosion, and corrosion.
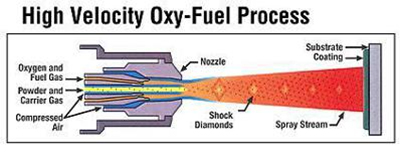
HVOF
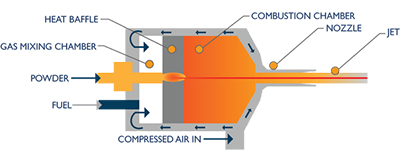
HVAF
HVAF and HVOF coatings can be used to improve the performance and lifespan of CNC machined parts in the oil and gas industry. Some of the benefits of HVAF and HVOF coatings include:
1. Corrosion Resistance: HVAF and HVOF coatings can provide excellent corrosion resistance to machined parts used in the harsh environments of the oil and gas industry. These coatings can protect the surface of the parts from exposure to corrosive chemicals, high temperatures, and high pressures.
2. Wear Resistance: HVAF and HVOF coatings can provide superior wear resistance to machined parts used in the oil and gas industry. These coatings can protect the surface of the parts from wear due to abrasion, impact, and erosion.
3. Improved Lubricity: HVAF and HVOF coatings can improve the lubricity of machined parts used in the oil and gas industry. These coatings can reduce friction between moving parts, which can lead to improved efficiency and reduced wear.
4. Thermal Resistance: HVAF and HVOF coatings can provide excellent thermal resistance to machined parts used in the oil and gas industry. These coatings can protect the parts from thermal shock and thermal cycling, which can lead to cracking and failure.
5. In summary, HVAF and HVOF coatings are advanced surface coating technologies that can provide superior protection to CNC machined parts used in the oil and gas industry. These coatings can improve the performance, durability, and lifespan of the parts, leading to improved efficiency and reduced maintenance costs.