Tool Steel CNC machining parts
Available materials:
Tool steel A2 | 1.2363 - Annealed state: A2 has high toughness and dimensional accuracy in hardened state. When it comes to wear and abrasion resistance is not as good as D2, but has better machinability.
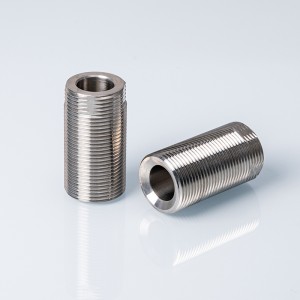
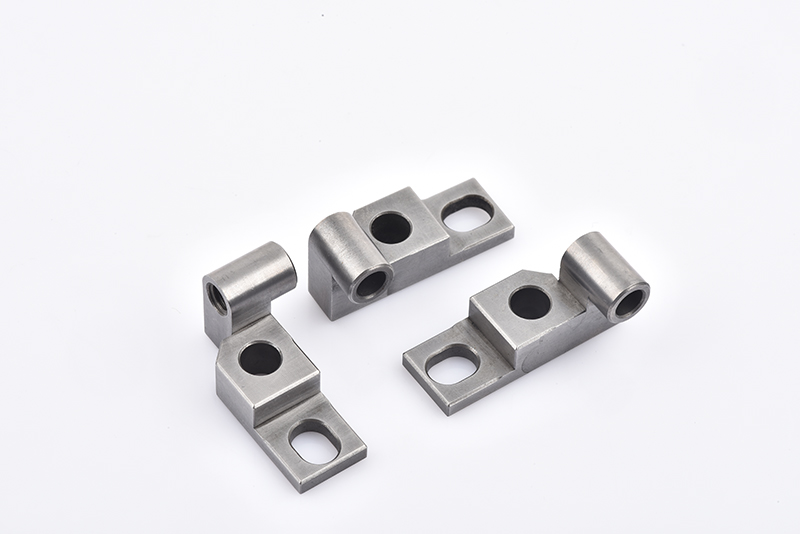
Tool steel O1 | 1.2510 - Annealed state: When heat treated, O1 has good hardening results and small dimensional changes. It is a general purpose steel that is used in applications where alloy steel cannot provide sufficient hardness, strength and wear resistance.
Available materials:
Tool steel A3 - Annealed state: AISI A3, is a carbon steel in the Air Hardening Tool Steel category. It is high quality cold work steel that can be oil quanched and tempered. After annealing it can reach hardness of 250HB. Its equivalent grades are: ASTM A681, FED QQ-T-570, UNS T30103.
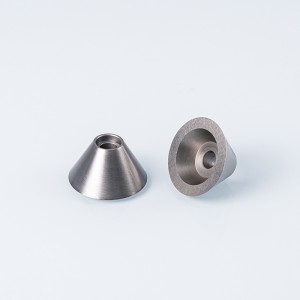
Tool steel S7 | 1.2355 - Annealed state: Shock resistant tool steel (S7) is characterized with excellent toughness, high strength and medium wear resistance. It is a great candidate for tooling applications and can be used for both cold and hot working applications.
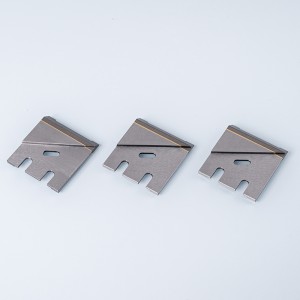
Advantage of tool steel
1. Durability: Tool steel is very durable and can withstand a lot of wear and tear. This makes it ideal for applications where parts need to be able to operate reliably for long periods of time without needing to be replaced in cnc machining service.
2. Strength: As mentioned above, tool steel is a very strong material and can withstand a lot of force without breaking or deforming during machine. It is ideal for CNC parts that are subject to heavy loads such as tools and machinery.
3. Heat Resistance: Tool steel is also highly resistant to heat and can be used in applications where high temperatures are present. This makes it great for making rapid prototype components for engines and other machinery that need to stay cool.
4.Corrosion Resistance: Tool steel is also resistant to corrosion and can be used in environments where moisture and other corrosive substances are present. This makes it great for making custom components that need to be reliable even in harsh environments."
How tool steel in CNC machining parts
Tool steel in CNC machining parts is made by melting scrap steel in a furnace and then adding various alloying elements, such as carbon, manganese, chromium, vanadium, molybdenum, and tungsten, in order to achieve a desired composition and hardness for assembly cnc parts. After the molten steel is poured into molds, it is allowed to cool and then heated again to a temperature of between 1000 and 1350°C before being quenched in oil or water. The steel is then tempered in order to increase its strength and hardness, and the parts are machined to the desired shape."
What CNC machining parts can use for tool steel material
Tool steel can be used for CNC machining parts such as cutting tools, dies, punches, drill bits, taps, and reamers. It can also be used for lathe parts that require wear resistance, such as bearings, gears, and rollers."
What kind of surface treatment is suitable for CNC machining parts of tool steel material?
The most suitable surface treatment for CNC machining parts of tool steel material is hardening ,tempering, Gas nitriding , nitrocarburizing and carbonitriding. This process involves heating the machine parts up to a high temperature and then rapidly cooling them, which results in the hardening of the steel. This process also helps to increase the wear resistance, toughness and strength of the machined parts.
What kind of surface treatment is suitable for CNC machining parts of stainless steel material
The most common surface treatments for CNC machining parts of stainless steel material are sandblasting, passivation, electroplating,Black oxide, Zinc plating,Nickle plating,Chrome plating,Powder coating, QPQ and painting. Depending on the specific application, other treatments such as chemical etching, laser engraving, bead blasting and polishing may also be used.